What is a Thermic Fluid Heater?
A thermic fluid heater, also known as a thermal oil heater, is an industrial heating system designed to transfer heat through a special type of heat transfer fluid (HTF), typically thermal oil, instead of water or steam. These systems are widely used across various industries such as textiles, food processing, chemicals, pharmaceuticals, and petrochemicals due to their high temperature capabilities and precise control.
Unlike steam boilers, thermic fluid heaters operate at atmospheric pressure, minimizing the risks associated with high-pressure systems while delivering consistent high temperatures — sometimes as high as 300°C to 400°C.
How Does a Thermic Fluid Heater Work?
Thermic fluid heaters work by indirect heating, where a burner or electrical heater heats the thermal oil. This oil then circulates through a closed-loop system, transferring heat to the desired processes. Once the heat is transferred, the fluid is recirculated back to the heater for reheating, ensuring maximum energy efficiency.
Key components of a thermic fluid heating system include:
- Burner or electric heater
- Heat exchanger
- Circulating pump
- Expansion tank
- Control panel
- Thermal fluid
Advantages of Thermic Fluid Heaters
1. High Operating Temperatures at Low Pressure
One of the most significant advantages is the ability to achieve high temperatures (up to 400°C) without pressurizing the system. This enhances safety and reduces maintenance costs.
2. Energy Efficiency
Thermic fluid heaters provide precise temperature control with minimal heat losses due to the closed-loop system. They also offer higher combustion efficiency and quicker response times compared to traditional steam systems.
3. Low Maintenance
Since these heaters operate at atmospheric pressure and do not involve water, problems like scaling, corrosion, or boiler blowdowns are eliminated.
4. Versatility
Thermic fluid systems are suitable for a wide range of industries and applications, including:
- Drying
- Melting
- Heating reactors
- Laminating
- Curing
- Baking
Types of Thermic Fluid Heaters
1. Horizontal Coil Thermic Fluid Heater
These are the most commonly used heaters. They feature a coil design that allows for uniform heating and compact installation. Horizontal heaters are ideal for continuous operations.
2. Vertical Coil Thermic Fluid Heater
Preferred when floor space is limited, vertical heaters offer the same functionality as horizontal systems but with a smaller footprint.
3. Solid Fuel Fired Thermic Fluid Heater
These systems use biomass, coal, wood, or briquettes as fuel. They are suitable for operations looking to reduce dependency on fossil fuels and cut operational costs.
4. Oil/Gas Fired Thermic Fluid Heater
Operates using furnace oil, LDO, diesel, or natural gas. These heaters offer automated control, clean combustion, and low emissions.
5. Electric Thermic Fluid Heater
Used in industries where fuel storage is a challenge, or where clean energy is preferred. These systems have zero emissions and lower noise.
Applications of Thermic Fluid Heaters in Industry
Thermic fluid heaters are extensively used in the following sectors:
- Textile Industry: For drying, printing, and dyeing operations.
- Food Industry: In edible oil processing, baking ovens, and food packaging machinery.
- Chemical and Pharmaceutical Industry: For jacketed vessels, distillation columns, and reactors.
- Petrochemical Industry: Bitumen heating, asphalt plants, and refineries.
- Rubber and Plastic Industry: In moulding machines, extruders, and calendaring lines.
Choosing the Right Thermic Fluid Heater
Selecting the ideal thermic fluid heater involves evaluating several factors:
- Heating Capacity (kcal/hr or kW): Depending on process heat requirements.
- Type of Fuel Available: Solid, liquid, gas, or electric.
- Temperature Requirements: Ensure the system can handle your maximum temperature needs.
- Flow Rate and Pressure Drop: Proper circulation ensures effective heat transfer and avoids pump overload.
- Space Availability: Choose between horizontal and vertical designs.
- Compliance & Safety Features: Overheat protection, emergency shutdowns, and explosion-proof components should be prioritized.
Thermic Fluids: The Heart of the System
The selection of thermal fluid is crucial to system performance. Some commonly used thermal fluids include:
- Synthetic Oils: High-temperature stability, suitable for up to 400°C.
- Mineral Oils: Cost-effective, suitable for temperatures up to 300°C.
- Silicone-Based Fluids: Excellent for extreme temperature ranges, chemically inert.
Always choose fluids with high thermal conductivity, low viscosity, and oxidation resistance. Regular testing and filtration are recommended to maintain performance and extend fluid life.
Maintenance Tips for Optimal Performance
To ensure long-term efficiency and safe operation, follow these essential maintenance practices:
- Regular Fluid Analysis: Check for oxidation, contamination, and viscosity changes.
- Leak Inspection: Monitor all pipelines and joints for potential leaks.
- Pump and Burner Checkups: Inspect for wear and tear and calibrate controls.
- Insulation Audits: Reduce heat losses by ensuring all components are well insulated.
- Safety Valve Testing: Ensure safety devices function properly under pressure surges.
Common Problems and Troubleshooting
1. Drop in Heat Transfer Efficiency
Cause: Degraded thermal oil or fouled heat exchanger.
Solution: Replace the fluid and clean heat transfer surfaces.
2. Overheating or System Shutdown
Cause: Malfunctioning thermostat or flow obstruction.
Solution: Inspect sensors and clear flow paths.
3. Pump Failures
Cause: Cavitation or air pockets.
Solution: Prime the pump and ensure proper fluid levels.
Future Trends in Thermic Fluid Heaters
With increasing emphasis on energy efficiency and carbon footprint reduction, modern thermic fluid heaters are becoming more intelligent with:
- PLC and SCADA integrations
- Remote monitoring
- Hybrid fuel systems
- Waste heat recovery options
These innovations not only enhance performance but also align with green manufacturing standards.
Conclusion
Thermic fluid heaters are indispensable in modern industrial operations requiring high-temperature heating. Their efficiency, low maintenance, and versatility make them a superior alternative to traditional steam-based systems. By understanding their operation, benefits, and maintenance needs, industries can maximize productivity while ensuring safety and energy savings.



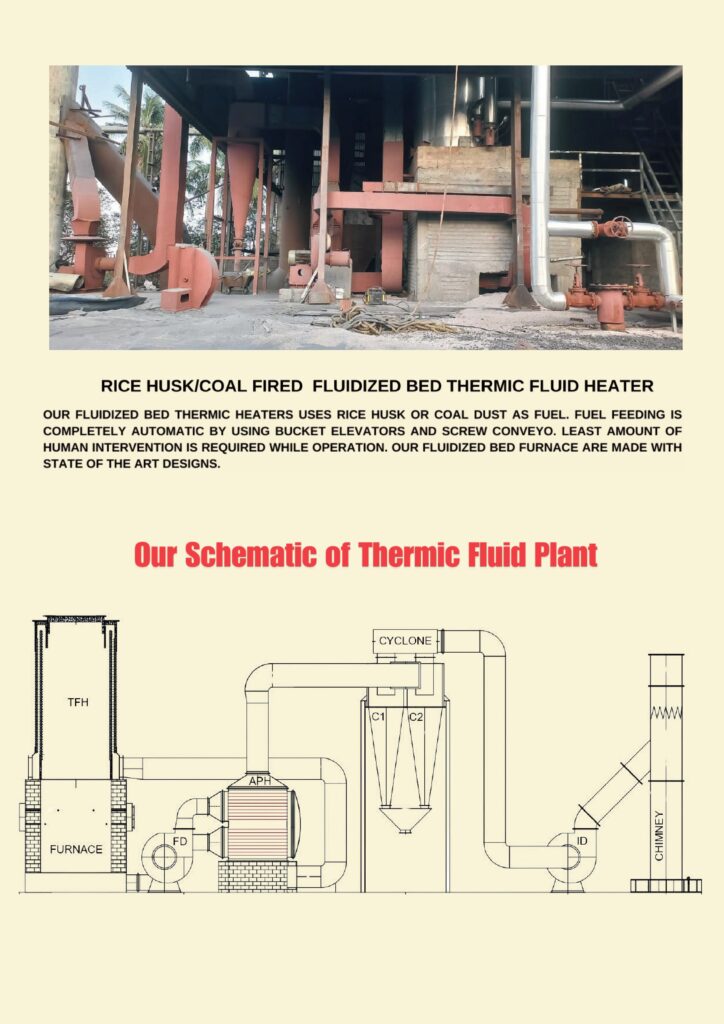